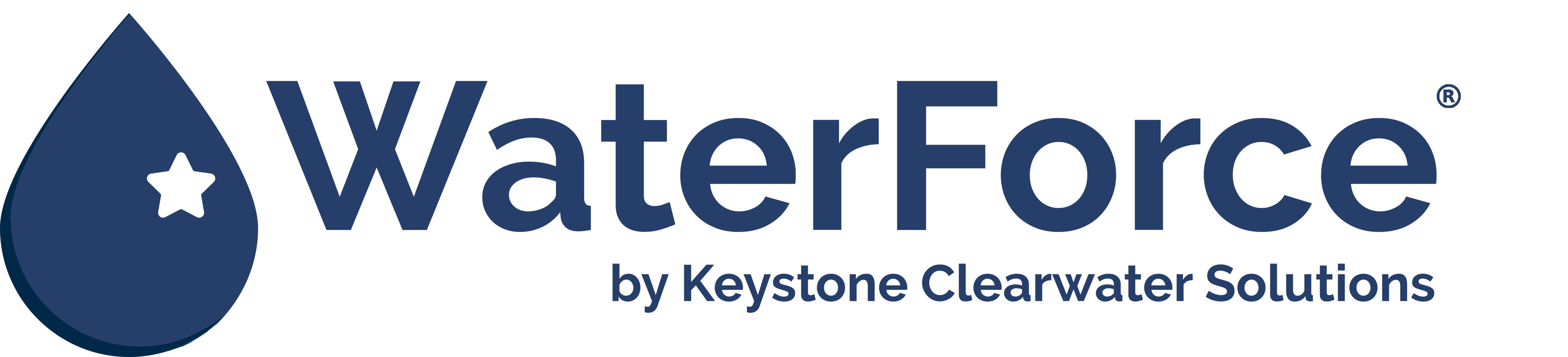
WaterForce: Fully autonomous water transfer for hydraulic fracturing support
Traditional water transfer automation packages typically feature a controllable pump package with pressure, flow rate, and tank level readings with an operator remotely controlling the pump package per the instrumentation feedback parameters. But Keystone Clearwater’s WaterForce® system takes water transfer automation project engineering to the next level.
For well completion operations in southwestern PA, Keystone Clearwater’s WaterForce® automation provided advanced pump and valve control system logic via Keystone’s proprietary MCU control skids – the core of Keystone’s rental automation offering. The flexibility of the MCU control skid and it’s onboard PLC allowed us to bring in inputs from other completions vendors and equipment on site, including wellhead valve positions and frac blender clean rates.
Our pump packages and valving systems transformed from a basic remote control to a fully automatic process. Several default run modes were programmed to handle deviations from normal run processes including automatic backup pump failovers, redundant valve actuation processes, and more. System safety interlocks included low- and high-pressure shutoffs, high tank-level based pump and valve shutoffs, pump RPM PID control, and system valving ESD processes.
System telemetry included cell and mesh radio redundancies and automatic failovers. Real time operational data was integrated into and shared with the customer’s centralized data suite, providing company personnel with a full view of up-to-date water transfer system information including system health checks and ready-for-next-stage status indications.
WaterForce water transfer automation improves efficiencies and safety
This successful fully automatic water transfer system deployment marked a significant milestone in the US well completions’ water transfer market. By advancing fast-deploy field automation capabilities, Keystone’s WaterForce® moved the needle on what is possible – towards a goal of eliminating manpower in safety-sensitive areas of the well pad during frac completions. These advancements enabled the onsite water transfer headcount to be reduced to one, as well as the cost savings that come along with reduced labor requirements. It also enabled system performance enhancements via M2M (machine-to-machine) processes because we were able to remove human error factors and verbal communication dependencies.
The SCADA operator’s role changed from an active controller of the pump and valving system to a passive monitoring system analyst. Finally, this fully automatic system gave our customer increased visibility to their operations allowing for efficiencies in cross-functional operational areas, including faster frac stage transitions and enhanced trucking logistics. To learn more about this case study and Keystone’s enhanced WaterForce® water transfer automation system, please contact Ed Strauser, Director of Automation.
Edward Strauser, PMP
Director of Automation