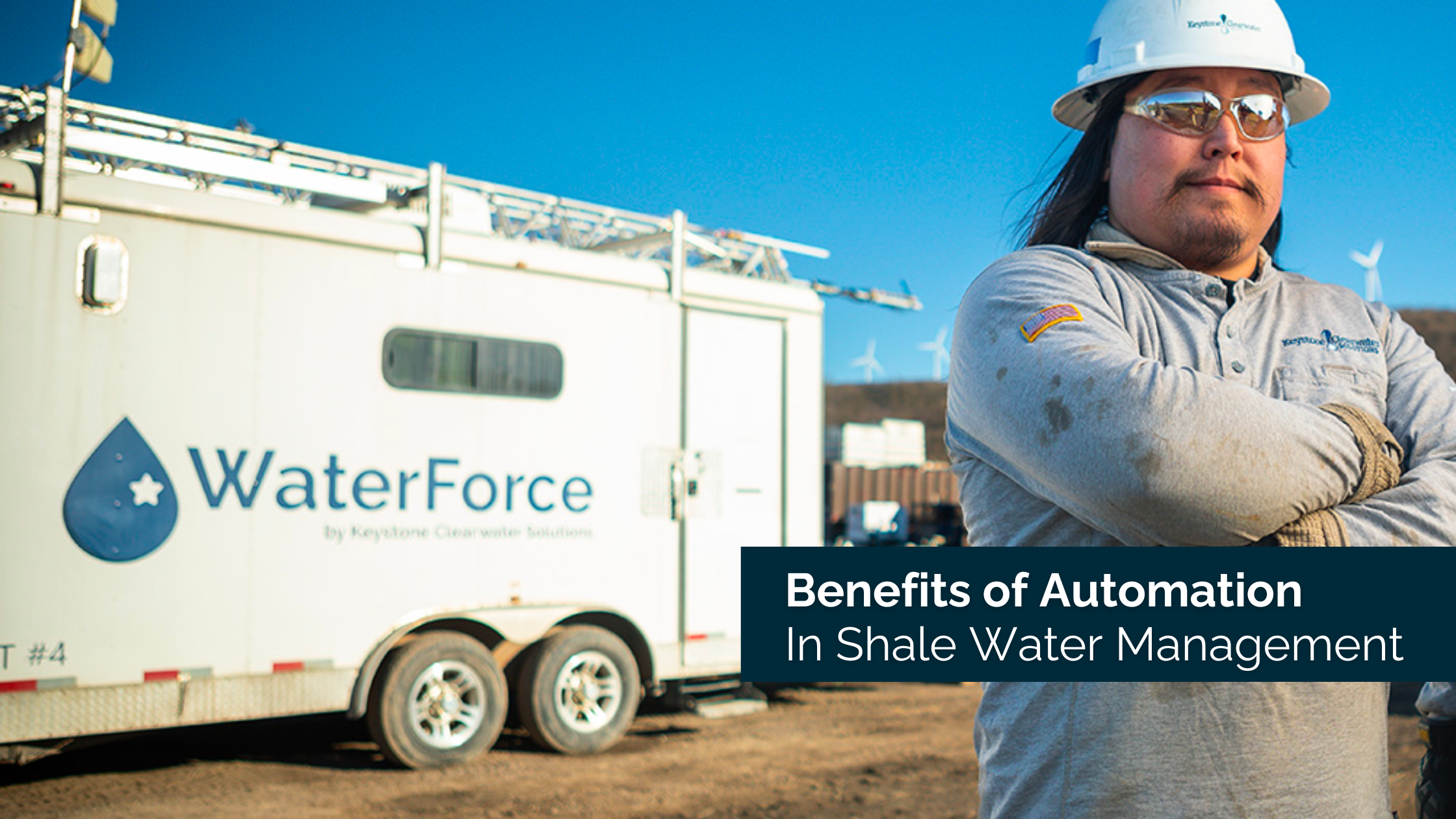
December 13, 2023
Benefits of Automation in Shale Water Management
Reduce manpower, improve safety, decrease costs, improve efficiency, maintain compliance
Shale gas extraction relies on a large amount of water and manpower during the process. Effective water management is vital not only to preserve this precious resource but also to keep costs down and workers safe, all while adhering to environmental regulations. Recent labor shortages have added to the challenges. Increasingly, operators are discovering the benefits of automation for shale water management.
Improved operations through automation
Using an automated systems provides multiple benefits, including:
Fewer staff
Before WaterForce automation, jobs would require between 6 and 20 employees per shift to run pumps, watch tanks, monitor flowrates/pressures, and oversee the project. With an automated system, the operations can be reduced to a couple employees, depending on the operator’s comfort level and the inspection and oversight that is necessary to keep pumps fueled, lines inspected, and systems running smoothly.
Reduced injuries
Because there are fewer employees working on-site and in potentially dangerous high-pressure areas, the chance of injury is greatly decreased. Employees can operate the project outside of danger areas or even completely off-site from another pad or from an office. With tank levels, flow readings, pressures readings, and pump controls all being run from a computer, slips, trips, and falls virtually disappear from daily operations.
Decreased environmental issues
Using system interlocks (shutdowns) and alarms significantly lessens environmental impacts from spills, tank overflows, and line blowouts. By automatically shutting down a pump when a pressure or high tank level event occurs, we reduce avoidable environmental impacts and costly downtime. By having these shutdowns automated it also reduces the human error element from the operations by having the system make decisions of when to shut down a line.
Improved system performance
The best part of an automated operation is that it doesn’t have sick days. The system does exactly what it has been programmed to do – every time, every day. To further remove the element of human error from the system, WaterForce is locked out from operating until the Managing Director has reviewed each interlock and signed off that our safety system is configured for the project. Implementing checks and balance system has improved performance and even further reduced issues for our customers.
Better water management efficiency
The WaterForce® program logs system information up to every second for pump health, line pressures, pumping rates, pump status, tank levels, water temperature, ambient temperature, and communication quality. This collected data is used to create reports for our customers, such as volume pumped and pump hours. It is also analyzed to improve system performance and to prevent issues from recurring. This data has been invaluable in analyzing incidents to figure out what happened and how we can use WaterForce to prevent the same incident from happening again.
Maintains regulatory compliance
Some water management tasks can be tedious but important and necessary to maintain regulatory compliance. Automation is ideal for these tasks.
For example, surface water permits limit how much water may be withdrawn from the source river. Without automation, a worker would have to be staffed at the site to monitor the stream gauge and the pump. If the stream level gets too low, the worker must shut off the pump to maintain compliance.
With the WaterForce automation system, water management is integrated with regulatory data websites and the USGS river gauge system to automatically shut down the pump to ensure regulatory standards for that area are not violated. If the level happens to come back up at, say, 2:30 am, the system can immediately begin running the water withdrawals rather than having to wait for a worker, who may not get on site until 6 am, to start the pumps again. This saves on the cost of manpower, improves worker safety, and enables more precise shale water management.
Expert water management solutions for the oil and gas industry
Keystone Clearwater Solutions was the first water transfer company in the Utica/Marcellus Basin to execute an entirely autonomous water transfer system on a customer’s completion job. The WaterForce system initiated the startup based on a signal from the wellhead and then ran autonomously based on inputs from the Data van and the automation sensors, pumps, levels, and valves on location. Essentially, the operator’s role transformed from a remote control operator to an analyst monitoring the project.
With our SCADA system, our customers can see what our team and operators see. We are able to give full access to our system for read-only views of our controls with the ability to receive live alert texts and emails based on system setpoints. Our customers also have access to all of our data collected on their projects, which can be used to analyze performance and optimize operations.
Learn more about the WaterView Realtime Reporting Dashboard and Data Analytics Suite.
WaterForce Automation Team
Over the last 6 years, Keystone Clearwater Solutions has heavily invested in our automation assets and in our Automation Team. Our in-house programmers created our SCADA system from scratch, and they work hard to keep all systems running correctly and to constantly improve safety and features. Our trained Field Technicians are available 24/7 to support operations, including mobilizing assets, troubleshooting electrical systems, setting up networking communications, configuring instrumentation and control devices, and deploying our WaterForce system.
Keystone Clearwater Solutions
With an experienced workforce and a full range of equipment and services, including WaterForce automation, we help customers with solutions that improve efficiency, save on costs, and maintain regulatory compliance. Keystone Clearwater Solutions has the assets to serve the water management needs of oil and gas operators in the Mid-Atlantic region and Texas. Contact us today at 717.508.0550 (Mid-Atlantic) or 432.552.8406 (Texas) for details.
For more information contact: Luke Beachy, VP of Automation at Keystone Clearwater Solutions. 717.508.0550. lbeachy@keystoneclear.net