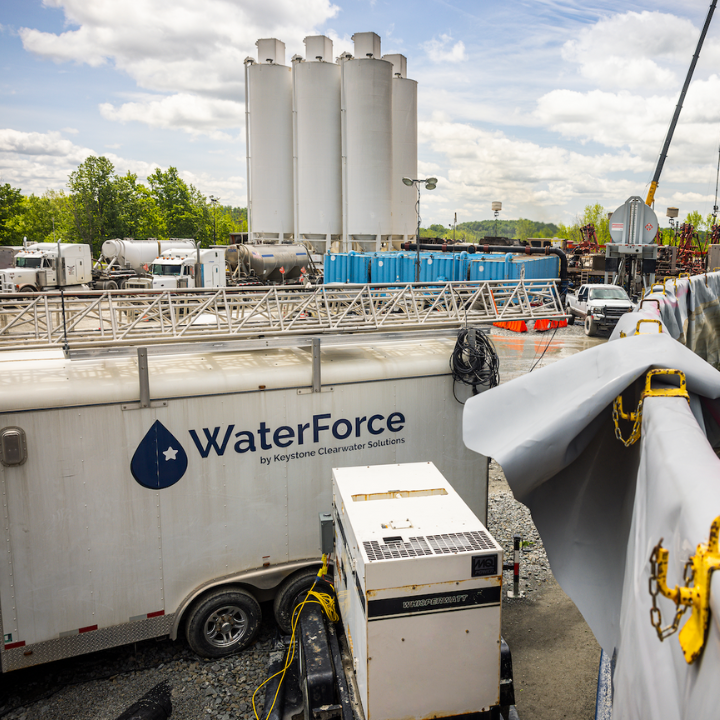
October 13, 2022
Water Transfer Automation Reduces Costs, Improves Performance
WaterForce: Water Transfer Automation Reduces Costs, Improves Performance
WaterForce, Keystone Clearwater Solutions’ proprietary water transfer automation system, can reduce costs, improve efficiency and reliability, and enhance safety and communications. With sites located in remote areas, often miles from water sources, automation helps ease challenges such as workforce shortages, regulatory compliance, and performance and safety issues.
Save money
One of the primary reasons for choosing a water transfer automation system is reduced costs. The reliable automated water transfer management that WaterForce provides means that on a jobsite typically requiring 5-7 employees, the process now can be handled by only 1 or 2. Staff reduction saves not only the cost of wages, but also benefits, training, and hiring expenses. Since the pandemic, there has been a workforce shortage in the industry, especially for hourly workers that work in extreme conditions monitoring tanks and operating pumps and valves. Waterforce handles these tasks 24/7/365.
Increase safety
Of course, employee safety is also a major concern. WaterForce operates in the toughest remote conditions, around the clock through all kinds of weather. This reduces the number of employees needed to work in safety-sensitive areas and enables the operator to focus on quality control from the comfort of a command trailer.
Improve quality
Data sent to a central location can be used to analyze the process, ensuring alarms and alerts receive appropriate responses, and to track the integrity of equipment and data reliability. Critical information about operations is passed to the customer in automated emails. Instead of paper reports or emails from 4 different employees across multiple shifts, data is consolidated and streamlined into one daily email. This allows greater insight into the water transfer process as a whole while reducing the time spent on administrative tasks.
Enhance efficiency and regulatory compliance
Water transfer automation helps improve efficiency of the process while ensuring water is being managed in accordance with regulations. WaterForce connects to and integrates with regulatory data sites (such as the USGS river gauge system) to inform its actions and maintain compliance. For instance, If the system is nearing the limit to how much water the customer is allowed to draw, WaterForce sends alerts and automatically shuts down the pump, avoiding a breach in compliance of regulatory standards for that area. This eliminates the need to have an employee watch passbys and shut the system down manually. It also ensures that the moment the water source level is permitted to start pumping again, WaterForce will initiate the system, even if it is 2:30 a.m. For customers in a water sharing agreement (with another company, municipality, county, or the state), automation ensures that the system only pumps the allotted amount per day, sending automated reports with metered totals.
Solve communication challenges for smooth water transfer automation
“Communication is probably the Achilles heel of any automation of water transfer system because the equipment as a full system isn’t all located on one pad, on one well site. It can be geographically challenging to run the equipment and pumps along a hydraulically profiled transfer line in the Northeast that is miles long, let alone communicating to these pretty remote areas,” said Edward Strauser, Director of Automation for Keystone Clearwater Solutions.
That’s why WaterForce has best-in-class communications for water transfer automation, featuring not only cellular and satellite service (including traditional VSAT and global internet systems like Starlink), but also fiber optic and Point-to-Point mesh radio capabilities. And Waterforce has redundancy in the telemetry to help ensure interruption-free operations. This includes automatic failovers and failbacks, such as between cellular service and satellite, and dual SIMs to increase cellular network service reliability.
In addition, WaterForce features PLCs (programmable logic controllers) on the pump. The advantage of being able to execute logic directly onsite, rather than through a central cloud-based system, is that in cases of communication difficulty, predetermined commands can easily be executed at the pump to keep operations running smoothly.
WaterForce in action: a first for Utica/Marcellus water transfer automation
“We believe we are the first water transfer company, definitely in the Northeast in the Utica/Marcellus region but possibly the first in the whole country, that was able to execute a completely autonomous water transfer system on a customer’s completion job,” said Strauser. An operator initiated the start-up of the system at the beginning of the job and then WaterForce took over. It was able to automatically turn on components, ramp up, ramp down, open valves, and close valves, all based on inputs from the other vendors onsite coming into WaterForce. Strauser added, “The inputs provide data to inform our system’s decisions, which are all done automatically, as opposed to remote control of these pumps and valves and the actual reading of a level sensor (or a flow meter or a pressure sensor) value by an operator making adjustments. WaterForce was able to respond to all of those inputs automatically, so then the operator’s job turned from essentially a remote-control operator to a systems quality analyst.”
For more about WaterForce, check out the case study or contact us to see how WaterForce can benefit your water transfer project.